Materials Science Plus Sustainability Equals Profits in a Circular Economy
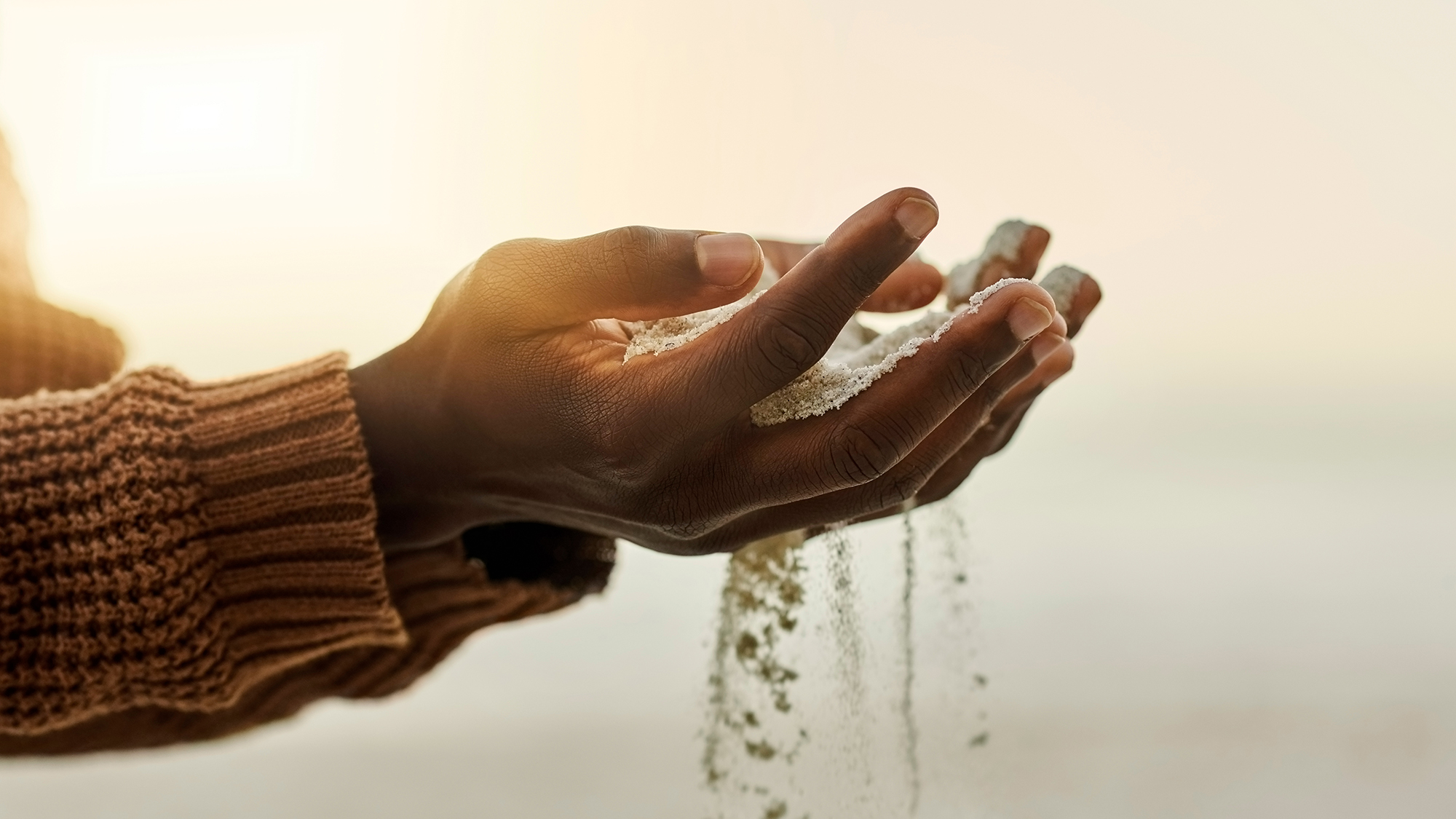
According to McKinsey, materials contribute 20% of the world’s greenhouse gas emissions to the atmosphere. Decarbonizing materials through substitution, developing new, less polluting materials, reusing spent materials and recycling what can’t be reused is the sustainability strategy that companies both large and small have used globally to streamline operations and boost profits. As governments lag in implementing environmental protection regulations meant to curb greenhouse gas emissions and mitigate the worst effects of climate change, business now takes the lead with impressive results.
Materials science got a boost in 2011 with the Materials Genome Initiative in the US, where scientists used AI to help accelerate the mapping of millions of potential combinations of elements to derive different materials for development and manufacture. Combined with tools that enable fabrication at any scale, this research and development sector is growing rapidly. Another goal of the Initiative was to break down siloes in the private sector and foster greater collaboration and innovation.
Sand, Carbon and Lithium
If you had to choose the most essential material for modern life, what would you choose? Plastic? Oil? Maybe you’d say lithium, knowing that the future of electronic devices hinges on this soft metal. But you’d be wrong. It’s sand. And there’s a global shortage of it. It turns out that not all sand is created equal. That, for instance, sand from the desert is too fine and smooth, ultimately too brittle, for construction. The builders and manufacturers need wet sand, and as demand increases, illegal mining leads to deep corruption and even murder. Construction booms in China fueled the use of more sand in four years than the United States used in the 20th century. In addition to destroying entire ecosystems on the ocean floor, sand mining is changing water circulation patterns.
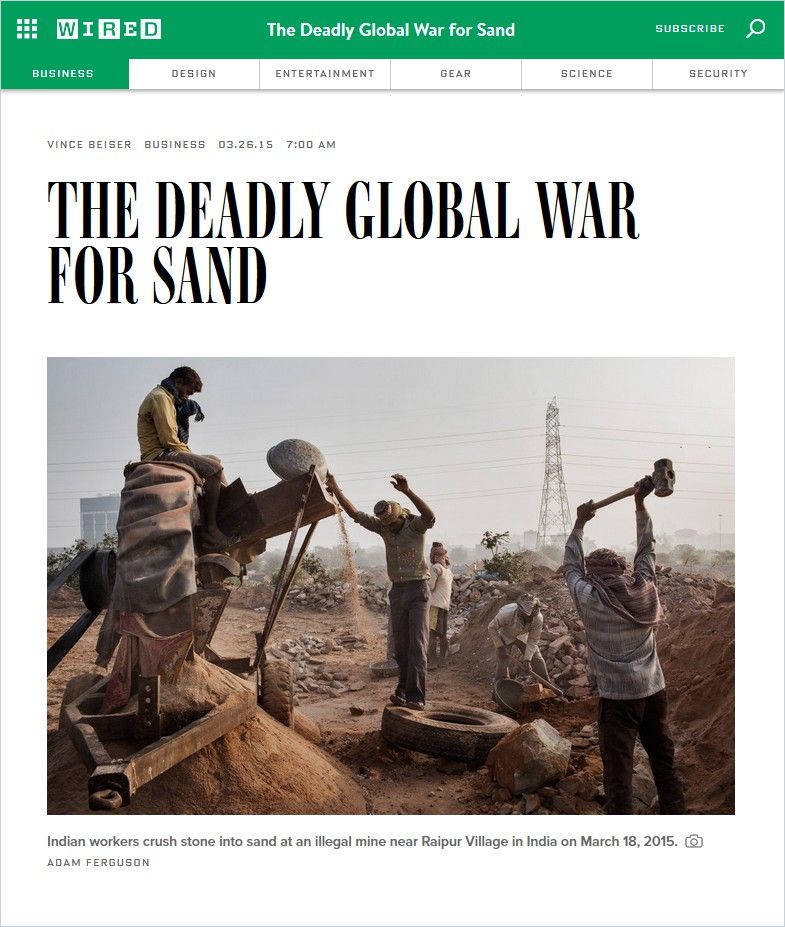
In The World in a Grain, author and journalist Vince Beiser writes about the ubiquitous nature of sand. It is everywhere: our buildings, in glass, in the sidewalks and roads, and in the computer chips designed by Silicon Valley – whole industries are founded on sand. Its purified form, silicon, made the digital revolution possible.
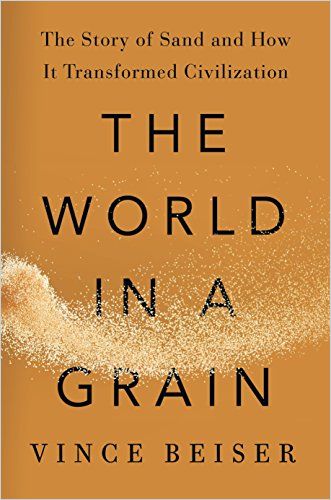
Natural gas fracking also uses sand mixed into a high-pressure slurry with water and chemicals to flush hydrocarbons hidden in pockets of shale: the sand keeps the cracks open in the fractured rock. According to Beiser, fracking uses more sand than buildings, glass and semiconductor chips. Sand mining severely degrades environments; in many cases, beaches have to be replenished by sand mined elsewhere. Countries like Dubai and China are building new islands from dredged sea sand, destroying ecosystems and, in China’s case, raising geopolitical concerns as they build military bases on them.
Though the supply might seem endless, sand is a finite resource like any other. The worldwide construction boom of recent years – all those mushrooming megacities, from Lagos to Beijing – is devouring unprecedented quantities.”
Vince Beiser
While the Earth is running out of sand, an overabundance of carbon fuels climate change at a breakneck speed. Carbon is a fundamental element for humans and all life on the planet. Scientist Robert M. Hazen writes in Symphony in C about the “carbon cycle,” the natural way carbon cycles continuously through the Earth, the air, the oceans and all living things. Fossil-based fuels burned at massive scale emit enormous amounts of carbon into the biosphere, which disrupts the natural carbon cycle.
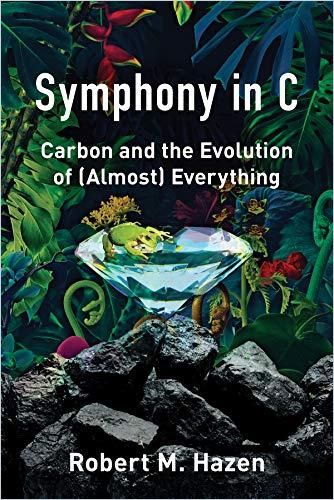
Carbon is a versatile atom, capable of forming stable bonds with many other kinds of atoms to create materials with unique characteristics. While highly compressed carbon becomes diamonds deep below the Earth’s surface, closer to the crust, carbon crystals form graphite, known best for its use in pencils. Graphite is made of layers of graphene, and graphene is a game-changer when it comes to new materials.
No chemical element plays the combinatorial game of bonding to other atoms better than carbon, whose chemistry is so unfathomably rich that scientists who spend their lives studying carbon have been given their own collective noun: ‛organic chemists’.
Robert M. Hazen
Graphene, an allotrope of carbon one atom thick that forms in a sturdy honeycomb pattern, is strong and flexible. Scientists can use graphene to add tensile strength and flexibility to other substances, creating, for instance, 3-D printed structures that can bear 10 times the weight of steel while being itself ultra-light. Using graphene in concrete makes it stronger and more water resistant, and by using less traditionally composed concrete, lowers carbon emissions.

Science writer Keith Veronese reports in Rare on the exotic elements indispensable to a global digital society. Conflicts over supplies of these metals drive up the costs of digital products. Though not technically considered rare, lithium is so crucial to producing electric vehicle batteries that the competition for mining commercial-grade deposits is fierce. It’s also expensive and carbon-intensive. Without international protocols for recycling lithium-ion batteries, the pollution from mining and from battery waste will proliferate. More modular designs will make these batteries easier to disassemble and recycle, saving energy and water in their refining and drastically reducing their carbon footprint. Better yet, say experts, figure out ways to reuse them. New designs for nuclear power plants now take advantage of a fraught waste material: spent radioactive fuel.
Nanotechnology and Programmable Matter
More sustainable materials are beginning to reduce the carbon impacts of multiple industries. Scientists created a synthetic tooth enamel that, beyond dentistry, holds manufacturing potential as a non-conductive material in computers, and, on a larger scale, for building earthquake-proof structures. Nanotechnology already improves materials, for instance, stain-resistant clothing and scratch-proof computer screens. It’s possible that manufacturers will soon be able to program matter to create material composites that change size or shape. Biosciences professor Kelly Weinersmith, author of Soonish, invites readers to imagine a future where homes are able to reconfigure themselves. Programmable matter combined with strong, flexible materials like graphene 3-D printed in optimal geometric configurations is just around the corner. Graphene’s conductivity and malleability make it an ideal solution as a lightweight, flexible pacemaker.
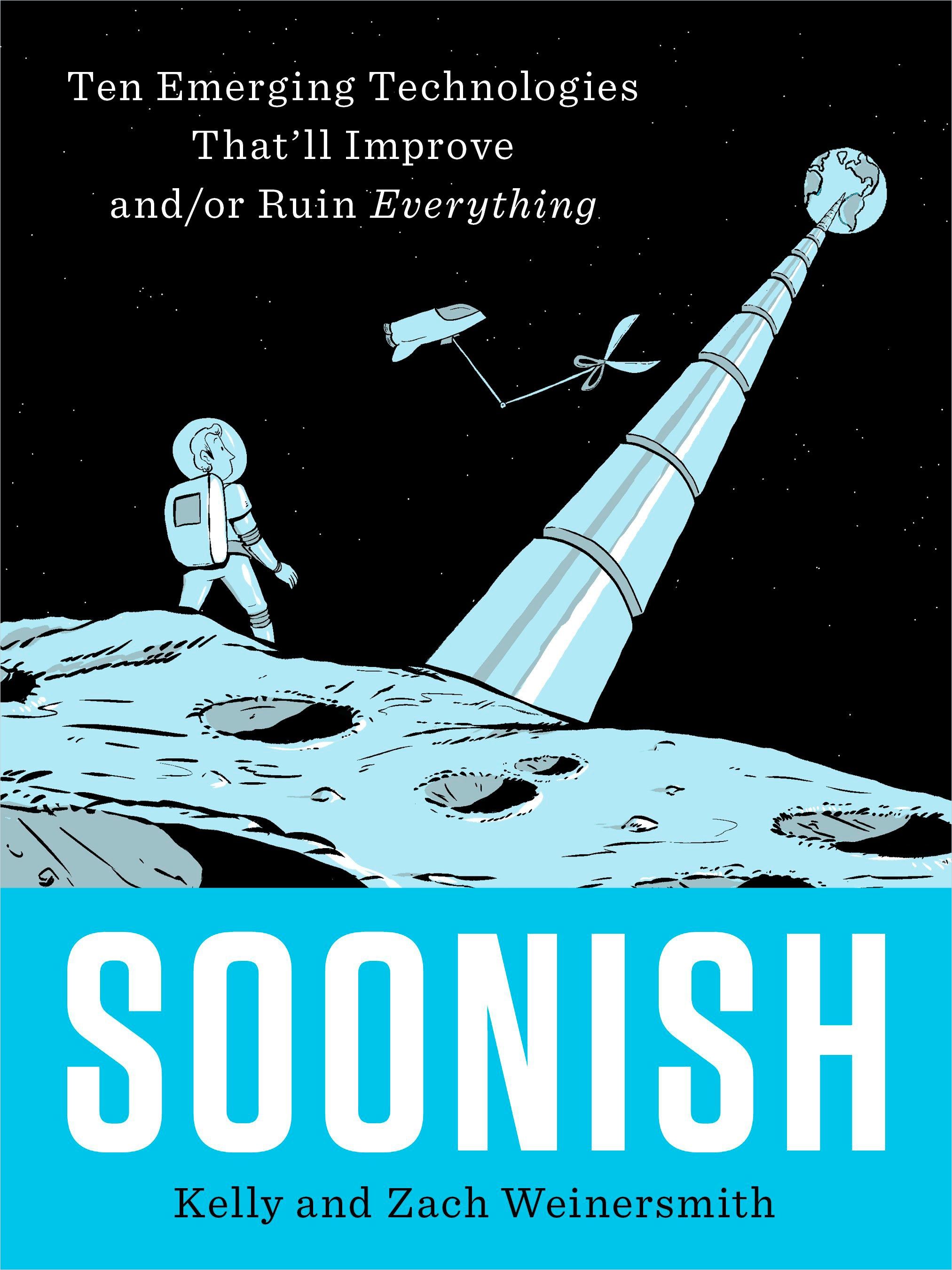
Weinersmith cautions that programmable matter comes with the same increased vulnerabilities for hacking as all “smart” objects. Criminals might reconfigure ordinary items into weapons, for instance. Programmable building materials extruded by large 3-D printers with AI assistance promise to lower the costs and timetables of construction. Homes built in this way could reduce carbon emissions and make housing more affordable for everyone.
Designing For a Circular Economy
A “circular economy” is a zero-waste economy where the by-products of manufacturing have usefulness as inputs for other purposes. For instance, Adidas recycles plastic pollution to manufacture sneakers. Thinking in terms of circularity adds jobs at every point along the value chain. Principles behind design solutions for sustainability include longer-term thinking, expanding the life cycle of products, offering products as a service, sharing best practices and updating industry standards.
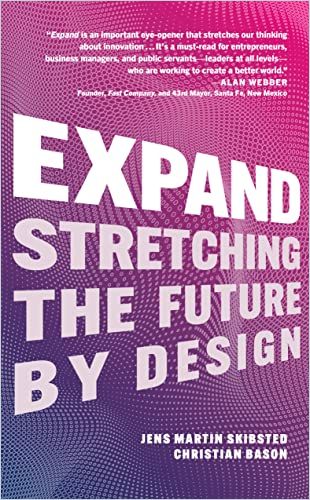
Thinking about the end of life cycle of materials has led designers to fuse natural systems with manufactured products. Mycoworks, for instance, uses mycelium from mushrooms as a substitute material for packing foam and leather goods. Swedish cement maker Degerhamm incorporates photosynthesis using algae to filter out toxic gases and leave behind oxygen. They then sell the algae as a component for agricultural feed. Only recently have estimates about material costs included their embedded energy. By gradually improving the recyclability of materials or substituting older, more carbon-intensive materials with lighter-weight, longer-lasting, less-polluting ones, industry gradually dematerializes problematic materials.
Can we extend the life of a material…so it continues to be productive and valuable with a new life cycle, and to become even more valuable in the next life cycle?
Founder of Miniwiz, Arthur Huang
Since the 1980s, the US has shipped much of its recyclable trash to China where it fueled several industries. But now China and other Asian countries have limited the quantities while raising their standards on the kinds of trash they will accept, according to PolyMatter.
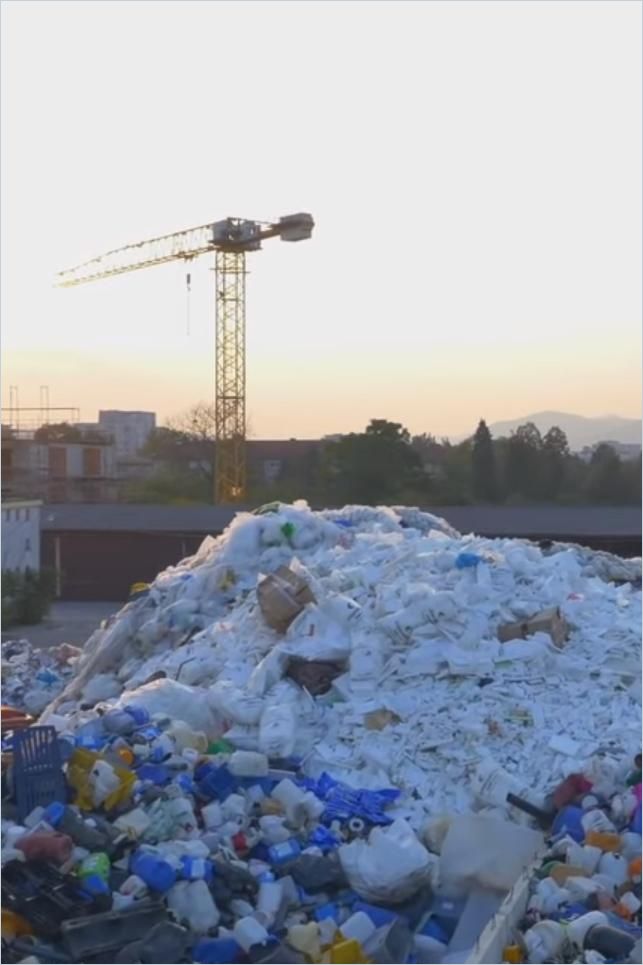
This forces the US to get smarter about its own trash economy. China is on track to produce three times the amount of trash the US produces by 2030, and so does not need US trash as inputs for manufacturing.

In “Making Manufacturing Sustainable by Design,” a World Economic Forum white paper, the authors show how digital plus automated manufacturing technologies offer industries an opportunity to implement design thinking and realize efficiencies, boost revenues and at the same time reduce environmental impacts. Reuse, recycling and remanufacturing (Re-X) can help businesses decrease their enormous energy consumption and has the potential to reduce emissions by 98% compared to manufacturing using new materials.
How Walmart Became a Leader in Sustainability
According to energy policy experts Hal Harvey, Robbie Orvis and Jeffrey Rissman in Designing Climate Solutions, buildings draw 54% of all electricity, much of which is still generated by fossil fuels. Decarbonizing electricity would draw down carbon emissions across industries.
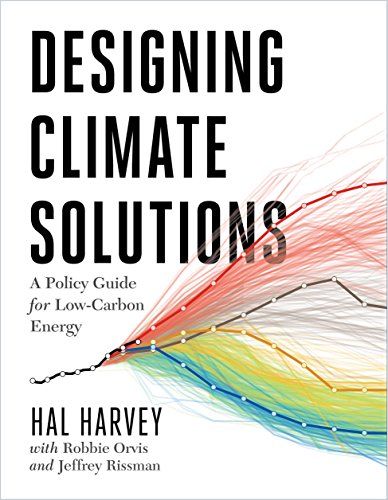
Industry is responsible for 38% of greenhouse gas emissions – some 19 billion tons – and as much as 50% of the energy used in industry is lost to heat. Hence, analyzing manufacturing processes for ways to reduce emissions, reuse energy and substitute or recycle materials makes financial sense and puts businesses on the path toward sustainability. This is exactly what Walmart did.
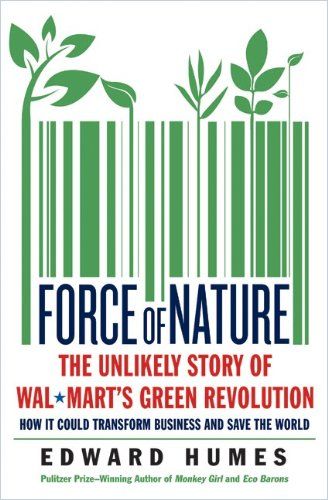
Then-CEO Lee Scott began a sustainability initiative that focused on improving three metrics:
- to transition to 100% renewable energy use.
- to commit to environmental sustainability, using its immense size and market share to clean up supply chains.
- to measure waste everyplace along the chains.
Scott involved people at every level in thinking about sustainability goals and gains. When a WalMart team described their goal as stocking shelves without toxic materials warning labels, they began the process of working with vendors to identify cost-effective non-toxic substitutes for dangerous chemical ingredients. Another team tackled measuring the carbon emissions associated with manufacturing each item. In this systematic way, WalMart reduced costs, streamlined its operations and redeemed its reputation with the public.
Read more about materials science, sustainability and a circular economy in the following summaries and Journal articles:
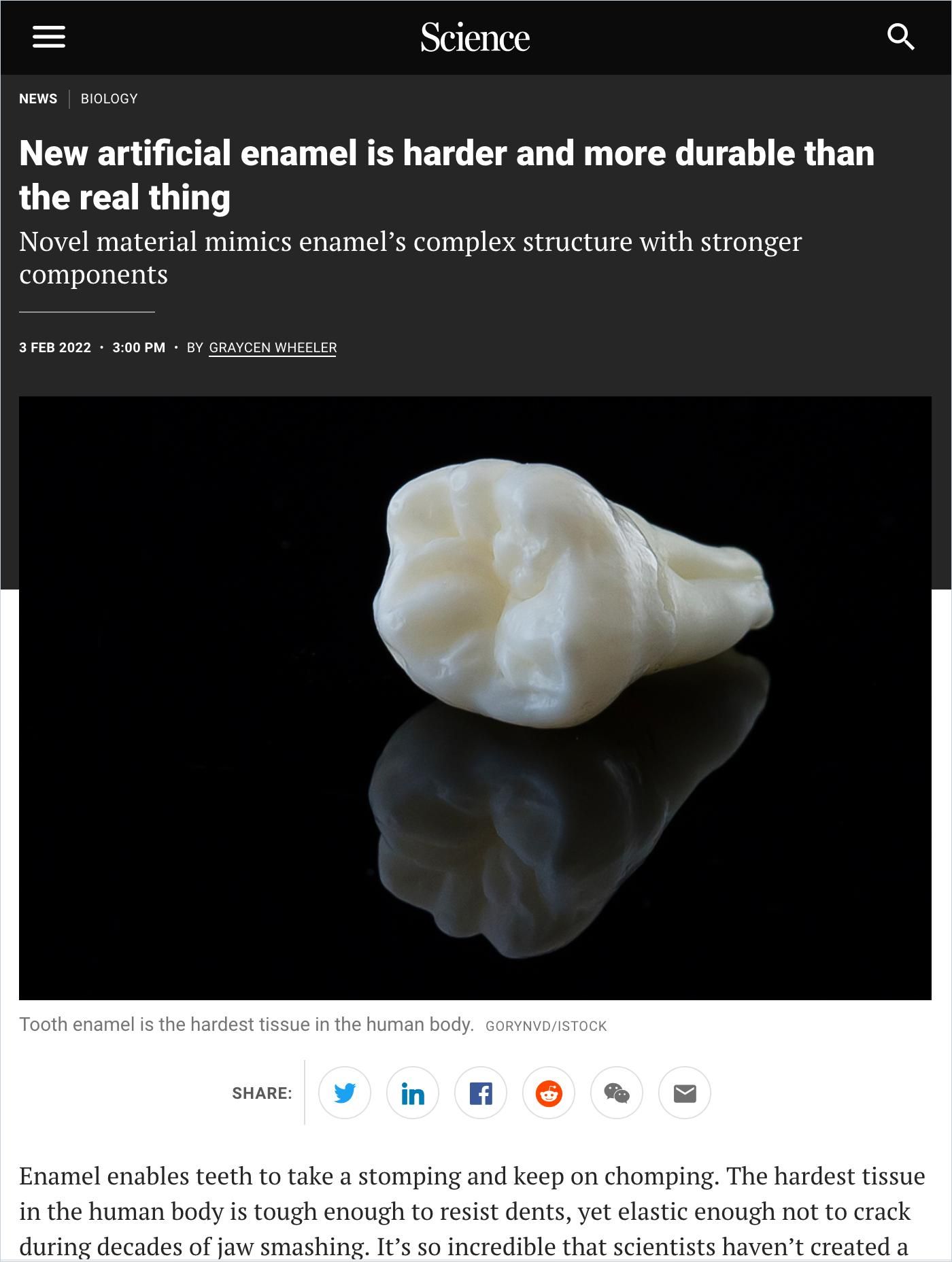